STAY CONNECTED
Signup for our blog to receive tips and knowledge on industrial wash and wastewater treatment best practices.
Work with Us
Don’t settle for less than a solution from a partner who takes complete responsibility from start to finish. We make it easy to keep things clean and compliance effortless. Contact us today to discuss your wastewater treatment and industrial wash needs.
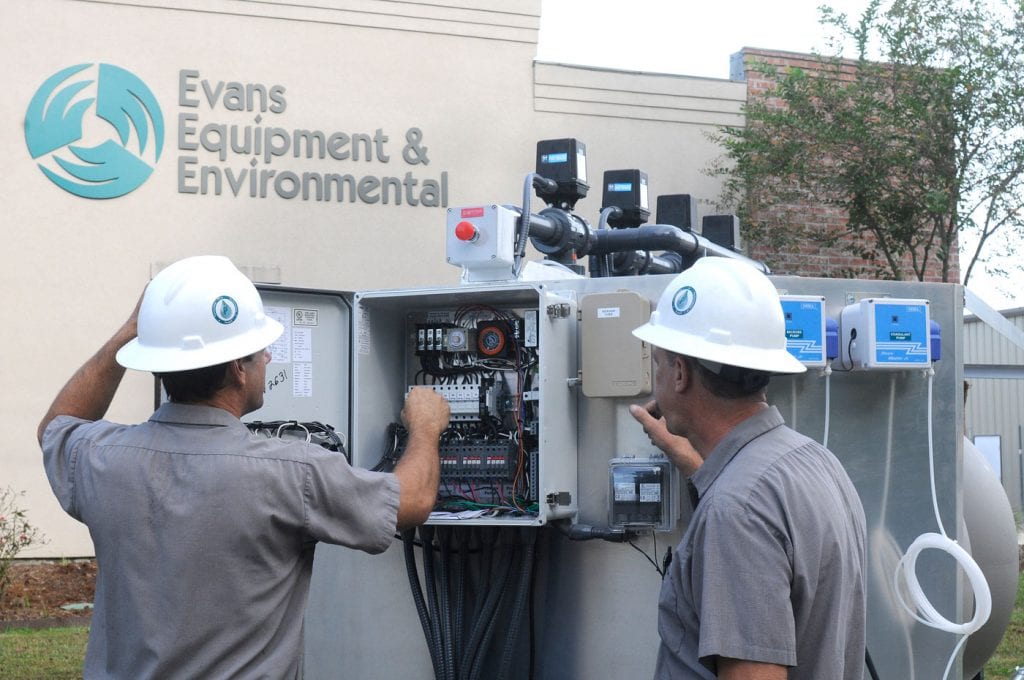
09/11/2018
5 Preventive Maintenance Tips for Industrial Wash Equipment
You may not love talking maintenance but you sure will appreciate the money it can save your business. Plant machinery is a significant investment that must be properly maintained if you hope to receive the maximum benefit and useful life.
Poorly maintained equipment costs more to operate over time, risks unplanned equipment failure, creates safety hazards, and threatens production. Conversely, a solid pro-active Preventive Maintenance Program will maximize the life and reliability of your plant equipment while lowering your total cost of operations.
One of our good customers recently shared that the production loss when our wastewater treatment system is out of operation is valued at $15,000 per day. This customer recognized that a minor repair on a Preventive Maintenance schedule would have saved significant cost in avoiding down time and likely been a less expensive fix if caught before failure.
Here are 5 tips to follow when developing a preventive maintenance plan for your industrial wash equipment:
1. Consider Equipment Availability
To the extent possible, you want to plan Preventive Maintenance for when the equipment demand is light. To minimize the impact of maintenance, take the time to think ahead and look at your production calendar for times that are best for maintenance to occur.
Additionally, consider the service duty of the equipment when planning maintenance frequency. Every company’s cleaning process is different. Usage time, size of equipment, and types of contamination dictate a variety of unique supplies and maintenance tasks to keep everything running smoothly. Higher frequency of use will require a more frequent maintenance schedule.
2. Keep the Right Materials Inventory
If you know production is about to get busy, work with your supplier to keep chemicals and spare parts in stock. Even 1-2 days without the right detergent or coagulant can cost your business unnecessarily. Your supplier can work with you to make sure you have the right amounts on hand for upcoming work.
Build your spare materials inventory list to support the preventive maintenance plan and in collaboration with your wash equipment supplier to be sure one of you has the material in stock when needed.
3. Get Your Employees On Board
To be most effective, Preventive Maintenance should be part of your business culture. It’s important that your employees are developing awareness and understanding of how operations impacts maintenance.
Maintenance supervisors and operations managers should develop an accountability system to make sure processes are in place to ensure your wash equipment is running well. One suggestion is to have a daily or weekly checklist that operators can complete to make sure equipment care is followed consistently.
4. Use Scheduled Maintenance as a Training Opportunity
When service technicians are on site, allow operational personnel to communicate with them. The better your employees understand the machinery, the more likely they are to think about potential misuse and breakage before it occurs. The more people that understand the needs of your unique equipment and setup, the better.
5. Keep All Service Documentation
After a service visit, make sure you keep a copy of what was completed and keep these for future reference. Understanding the parts and supplies that often need replacing will help you evaluate the effectiveness of your current maintenance plan and make any adjustments for the things you see requiring repair. Sharing the maintenance results with your employees will help them understand what to look out for in daily operation.
Evans Equipment & Environmental understands the cost savings that comes along with proper preventative maintenance on your equipment. Much like any piece of equipment, an ounce of prevention yields a pound of cure.
While Evans Equipment & Environmental designs its systems with the end user in mind and has an eye on minimal maintenance requirements, the equipment we provide must be regularly serviced for optimal performance.
Evans Environmental & Equipment is your Support Partner. We are proud of the equipment we provide and want to ensure your operation is able to produce with little to no interruptions. As such, the above case study at the beginning of this article could have been prevented through a simple, affordable preventive maintenance schedule. Call Evans Equipment today at 1-800-377-5872 to discuss the available scheduled maintenance plans we offer to keep you up and running!